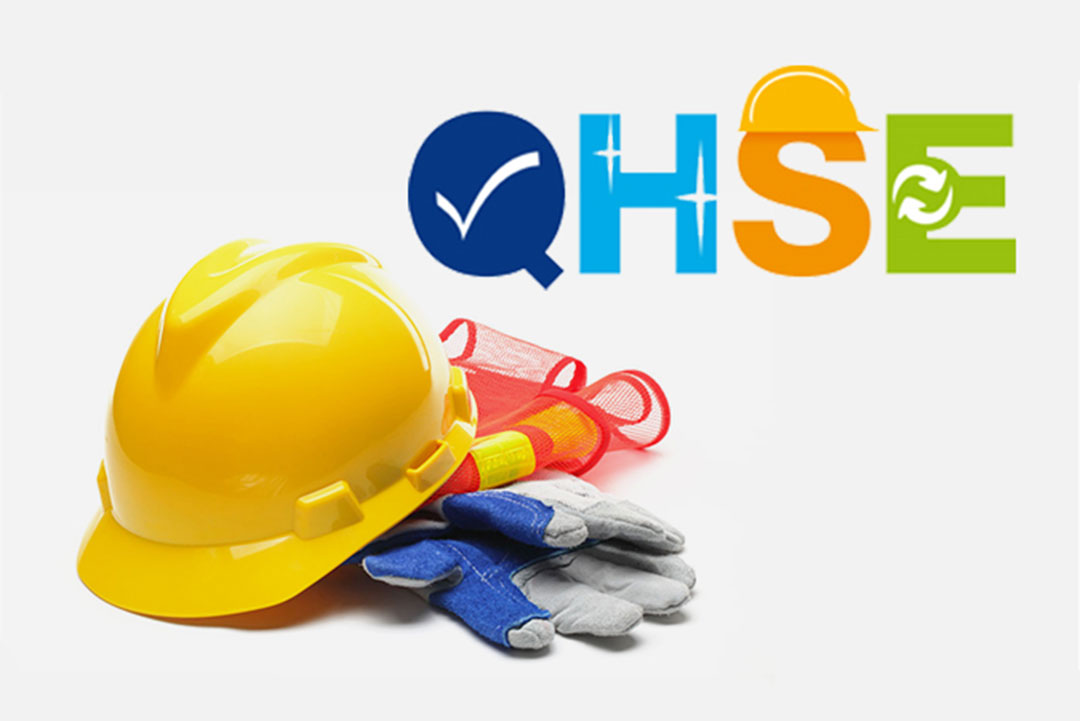
TRAINING Integrated QHSE Management System
The QHSE System Manager (Quality, Hygiene, Safety, Environment) defines and coordinates the “quality, health, safety and environment” policy for products, services and people across all the processes and structures of the company.
He negotiates with management, designs and implements methods and tools available to company departments for maintaining and improving quality, health, safety and environment management.
It is a support activity in the company and the QHSE system manager is above all a communicator who manages projects, coordinates actions and motivates company employees in order to meet customer and regulatory requirements.
FORMATION’S GOAL
At the end of the training, candidates are able to define the QHSE policy and negotiate the allocated resources.
They have acquired the necessary skills (development of procedures, methods and tools) for the implementation of the management system of quality, hygiene, health, safety and environment procedures and for its coordination.
They are able to verify the actions carried out, analyze the non-conformities identified, conduct audits and recommend the necessary readjustments.
Themes
1. INTRODUCTION TO LEAN MANAGEMENT
2. SAFETY DOCUMENTS
3. QSE DASHBOARDS
4. PSYCHOSOCIAL RISKS AND QUALITY OF LIFE AT WORK
Training content
- Mastering Lean tools to drive change
- Understanding the Lean Transformation
- Master the stages of Lean transformation.
- Plan the stages of change
- Identify the cultural, organizational and managerial changes necessary for the deployment of Lean
- Identify waste and organize to reduce it.
- Know the mandatory security documents during interventions managed by subcontractor
- Fill out the correct document depending on the situation: a prevention plan, a work permit, a fire permit, an internal driving license
- Manage the areas of quality, safety and the environment by defining your indicators
- Define effective dashboards
- Target your dashboards in relation to your objectives
- Set up and monitor your dashboards
- Define psychosocial risks, suffering at work
- Know the regulations and their responsibilities as a manager
- Knowing how to identify, analyze and evaluate PSRs: audit your organization to identify areas for improvement
- Acquire an RPS prevention methodology: know the manager’s levers of action
- Register RPS in the DUERP: put in place a sustainable approach to prevent RPS integrated into the overall risk prevention approach
- Develop an action plan
training duration
4 days
Public and prerequisites
- Prerequisite: Knowledge of occupational risk assessment is recommended.
- Audience: company manager, safety officer, quality manager or technician, team leader, works and operations manager.
Teaching methods & deliverables
- A practical exercise adapted to your contexts will be carried out in order to be as close as possible to your real situations.
- Standard security documents will be given to you.
Method of control of learning
A quiz in the form of multiple choice questions will be carried out at the end of the training.
Validation of learning
Training certificate.